Ready Mix Concrete Plant Certification Scheme
Quality of concrete being produced and used in construction has remained one of the major concerns of owners and specifiers. Unfortunately, till very recently, no established framework was available to ensure quality. The Ready Mixed Concrete Manufacturers’ Association (RMCMA) was the first to initiate efforts to evolve a framework for quality for ready mixed concrete. It was based on two strong pillars – best practices followed in advanced countries and adherence to provisions in the Indian standards. Two Quality Manuals prepared by an expert committee contain the details of the RMCMA Scheme. This plant audit-based scheme was launched in December 2008 and around 250 RMC facilities at 50-plus locations in India (mostly belonging to RMCMA member companies) were audited and certified by the RMCMA.
After operating this quality scheme successfully for nearly four years, RMCMA decided to raise the quality scheme to a higher pedestal. For this purpose, RMCMA signed a Memorandum of Understanding (MoU) with the Quality Council of India (QCI) – a non-profit, national apex organization wedded to quality facilitation, accreditation and surveillance.
QCI took the initiative of setting up three committees, namely, the Steering Committee, Technical Committee and Certification Committee. Experts from Multi Stakeholder organizations were invited to be the members of these committees. The involvement of these organizations in the evolution of the scheme ensured that the ownership is broad-based and comprises of representatives from major owners and specifiers in the country, using large volumes of concrete.
Three expert committees set up by QCI
The evolution of QCI scheme took more than one-and-a-half year. Three following painstakingly prepared Scheme Manuals were finalized by the expert committees.
Multi Stakeholder Ownership
- Central Government Ministries, e.g. Ministry of Housing & Urban Poverty Alleviation, Ministry of Road Transport and Highways, etc.
- Key Specifier: Central Public Works Department (CPWD)
- Central PSUs e.g. National Highway Authority of India, Airport Authority of India, etc.
- User bodies, e.g. Builders Association of India, CREDAI, Construction Federation of India, etc.
- Professional bodies, e.g. Indian Concrete Institute (ICI), Association of Consulting Civil Engineers (ACCE)
- Manufacturers, e.g. Ready Mixed Concrete Manufacturers’ Association (RMCMA), Cement Manufacturers’ Association (CMA)
- Certifying bodies, e.g. Bureau Veritas Certification (I) Pvt Ltd., ICMQ India Pvt Ltd.
The QCI Scheme conforms to the requirements of the Bureau of Indian Standards (BIS), Indian Roads Congress (IRC), Indian Railway Standards (IRS), etc. and is applicable for plants supplying concrete commercially, those supplying concrete for specific project, and plants supplying concrete partly on commercial basis and partly for captive consumption. Scheme excludes operations of placing, compaction, finishing and curing of concrete.
QCI Scheme Manuals prepared by multi-stakeholder committees
The QCI Scheme offers two options of certifications:
- RMC Capability Certification
- RMC 9000+ Certification
RMC Capability Certification is the crux of the QCI Scheme. Comprehensive criterion has been developed by the Technical Committee which is documented under the Scheme Manual “Criteria for Production Control of Ready Mixed Concrete”. Besides the audit of the plant and machinery and the control mechanism adopted by the producer, the criteria also embody laboratory testing facilities, technical skills of the human resources, the controls exercised on the quality of different concrete ingredients, mix design and the final product.
The production control criteria which can be considered to be heart of the scheme include the following six main features:
- Resource management: It covers three main areas, namely, plant, equipment and other utilities, laboratory and key personnel. Main areas under resource management are diagrammatically presented. Provision of basic laboratory testing facility is made mandatory in the QCI Scheme. The minimum testing equipment for the laboratory and the calibration frequency of the equipment are also specified. Compressive check list items have been developed so that an auditor is able to an in-depth understanding of all key aspects of resource management having bearing on quality.
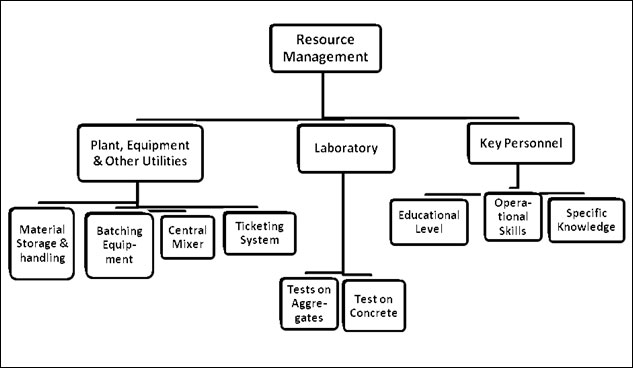
Resource management under production control criteria
- Control on Quality of Incoming Materials: The ready-mixed concrete producer needs to verify quality of all ingredients on a regular basis. Various standards of the BIS have specified the tests to be performed on different ingredients and their frequencies of testing. The QCI scheme has made it mandatory to perform these tests at BIS specified frequencies. It is also specified that the physical and chemical properties of the basic ingredients should be tested in an NABL-accredited laboratory, at least once in six months or when there is a change in the source of materials. Such rigorous testing regime would certainly ensure that ingredients having good quality are used in production of ready-mixed concrete.
- Concrete Design: The QCI scheme requires that the ready-mixed concrete producer should have in-house capability to carry out mix proportioning and adjustments in the mix to cater to the variability in the incoming materials – for example, the variations in the moisture contents in aggregates, etc. The competence of the key personnel who carry out mix design will be judged by the auditors by going through the old records, interviewing some key personnel and witnessing few tests in the laboratory.
- Production and Delivery: The auditor has been given the freedom to choose any five orders received by the producer during the past six months and verify from the autographic records as to whether the supplies have been made exactly as per the orders of the customers. Incidentally, the tests to be conducted and their frequencies in controlling the quality of the final product have also been specified in the QCI Scheme.
- Control on Process Control Equipment and Maintenance: Upkeep of plant and equipment, their calibration, etc. play an important role in determining the quality of the final concrete. The QCI scheme specifies the frequency of inspection, calibration tolerances, etc.
- Complaints and Feedback: The QCI Scheme has made it mandatory to have a Nodal Officer, who will be responsible for complaints and feedback. The scheme also highlights the importance of having established procedures to receive, resolve, review and find out the root causes of the complaints.
Certification Process
Detailed procedures for carrying out certification under the QCI Scheme have been evolved and are explained in the Certification Manual. The broad aspects covered under the procedures are as below:
- Application for certification: It includes application form, registration of applicant and the information to be furnished by the applicant to the certifying body.
- Audit program: The audit program is divided into Stage 1, Stage 2 and Surveillance audits. While each plant needs to be audited under RMCPCS, the ISO 9001 audits can be carried out on sampling basis as allowed under ISO 9001 certification.
- Audit man-days: Audit man-days under certification and surveillance audits for both schemes have been fixed by the Certification Committee.
- Audit planning: This includes the information to be provided to the certifying body, constitution of audit team and audit plan.
- Application for certification: It includes application form, registration of applicant and the information to be furnished by the applicant to the certifying body.
- Certification audit: It provides guidance on how RMC 9001+ QMS based certification and RMC capability certification audits should be performed. Safety measures to be adopted during the audit are also highlighted.
- Non-conformities: Three types of Non Conformity (NC) have been specified, namely, critical, major and minor. The detailed description of each of the NCs and the time for closure have also been specified. The CBs need to send the audit report within 7 days from the date of the completion of the audit.
-
Non Conformities – Description, classification and time frame for closure
Non conformity |
Description |
Classification |
Time frame for closure |
Critical |
Non compliance with a requirement which indicates serious failure of the plant’s capability to produce and deliver RMC to meet the customer requirements |
Check List items:
3.2.1.1 Storage –Cement only
3.2.1.2 Batching and Mixing
3.3 Laboratory
5. Concrete Mix design
6. Production and delivery
6.1 Identification and traceability
7. Control of process control equipment and measurements |
Within 15 days. Corrective actions shall be submitted to CB within 10 days. Onsite verification to be undertaken within 5 days and decision taken either to close the NCs or suspend certification |
Major |
Non conformity regarding a Management system requirement which does not allow the production and delivery process to meet the customer requirements (applicable to ISO 9001 requirements only as defined by CB) or as given in the Criteria for the classification in column 3 |
3.2.1.1 Storage –other than cement
3.2.1.3 Delivery fleet
3.4 Key personnel
4. control of incoming materials
8. Complaints |
Within 1 month. Evidences of closure shall be provided to the CB; verification to be done on site |
Minor |
Non compliance with a requirement which does not compromise either the overall management system effectiveness or the production and delivery process |
6.2 Control of non-conforming products
9. Feedback. |
Within 3 months. Evidences of closure shall be provided to the CB; verification to be done in the following surveillance audit |
- Certification decision: Certificate will be issued by the CB, only when all raised NCs are closed (critical and major after on-site verification and minor after off-site verification).
- Surveillance: Surveillance audits shall be carried out by the CB every six months, with at least one surprise audit in a year. The surprise audit will be conducted with a short notice of 3 days.
- Complaints: This section covers the complaint handling process. The need to have a documented process to receive, evaluate and make decisions on complaints is highlighted. The CB should audit the complaints received by the plant from its customers. The manner in which a complaint received about a certified plant should be handled is described.
- Certificate: The information to be included in the certificate as well as its validity are described.
- Suspension and withdrawal of certificate: It provides detailed guidance when the certificate will be suspended and withdrawn and the suspension will be revoked.
- Change of location/ownership/name: The certified plant needs to inform the CB changes in location, ownership and name of company. With the change in location, audit of the new facility becomes essential. In case there is a change in the name of the company or its ownership, appropriate documents need to be submitted to the CB.
- Fees: the fee structure of the CB shall be publically accessible and also provided on request.
Approval System for Certification Bodies
The Certification Bodies (CBs) which would be auditing and certifying the ready-mixed concrete plants under the RMCPCS need to primarily comply with the requirements specified in ISO 17065 and additional requirements specified by the Quality Council of India. With a view to commence the operation of the scheme immediately, a Provisional System for Approval of the CBs was evolved, documented and approved by the Certification Committee. Stringent requirements have been specified the committee for the CBs operating the scheme. The Minimum Competence Requirements of Auditors auditing the RMCPCS have been specified. Further, the CBs will be subjected to a through yearly audit. They need to obtain accreditation from National Accreditation Board for Certification Bodies (NABCB) under the QCI.
Minimum Competence Requirement of Auditors
- Minimum Bachelor’s degree in engineering in related field(s) with at least 5 years of relevant experience in RMC/Batching plant; or Diploma in engineering in related field(s) with 7 years of relevant working experience in RMC/batching Plants
- Experience in core technical processes like QA/QC or production and process control
- Training and experience in auditing.
Conclusion
The QCI Quality Scheme provides a comprehensive framework of controlling quality of concrete from ready-mixed concrete plants. The Key Benefits of the Scheme to owners/specifiers, RMC producers, small customers and concrete industry are highlighted.
Key Benefits of QCI Scheme
- For Owners and Specifiers (architects, consultants)
- Third-party quality assurance from an independent agency, based on well-defined quality norms evolved by experts
- Reliable Tool for short-listing of concrete producers
- For RMC/Concrete Producers
- Competitive advantage over non-certified producers
- Top management gets audited data on their plants
- Small Customer (e.g. individual house builder)
- Assurance on QA&QC of concrete, without employing experts
- Concrete Industry
- Raise the industry standard and bring it on par with those from advanced countries.